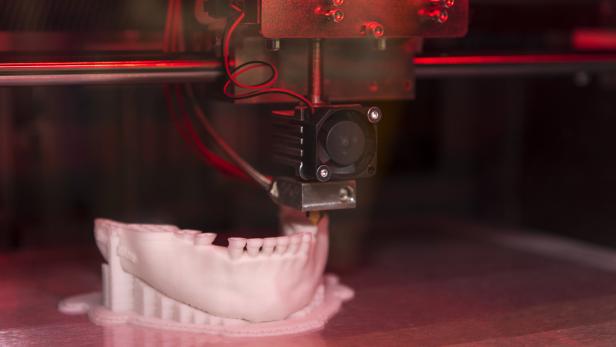
Maßgescheiderter Kieferknochen aus dem 3D-Drucker
Wie Forscher die Herstellung medizinischer Ersatzteile revolutionieren
Dieser Artikel ist älter als ein Jahr!
Stefan Baudis erzählt von seiner Vision: „Stellen Sie sich vor, jemand hat einen Unfall oder leidet an Tumoren. Betroffen ist der Kopf. In beiden Fällen kann es passieren, dass es Löcher im Kiefer oder im Schädelknochen gibt.“ An dieser Stelle kommt seine Forschung ins Spiel: „Idealerweise macht man vor der Operation einen CD-Scan der betroffenen Stelle. Die Daten werden ausgewertet, um ein maßgeschneidertes Ersatzteil zu berechnen, das dann im 3D-Drucker gefertigt wird.“
Baudis ist zufrieden: Vor kurzem hat er sein Christian‐Doppler Labor an der Technischen Universität (TU) Wien eröffnet: Gemeinsam mit drei Unternehmen – darunter der Weltmarktführer in Sachen 3D-Druck von Keramik – arbeitet er genau daran: Knochen aus dem Drucker.
Blaues Licht
Wer es genau wissen möchte: Die Technik basiert auf der Stereolithografie. Heißt: Licht spielt eine große Rolle. Blaues Licht, um präzise zu sein. „Innerhalb von Sekunden wird die verwendete Flüssigkeit dabei fest“, erklärt der Forscher vom Institut für Angewandte Synthesechemie, der das neue CD-Labor leitet. „Man braucht Photopolymere.“
Wer sich jetzt nichts vorstellen kann: Möglicherweise haben Sie so etwas im Mund. Kunststoff-Füllungen beim Zahnarzt sind daraus gefertigt. „Im Gegensatz zum Zahnarzt haben wir einen ganz anderen Ansatz. Der Zahnarzt füllt die Flüssigkeit in ein Loch und härtet sie aus. Das Material bleibt im besten Fall ein ganzes Leben dort drinnen. Wir brauchen aber ein Material, das sich abbaut. Das Gewebe soll dort hineinwachsen.“
Baudis ist in seinem Element und erklärt: „Im System Knochen gibt es zwei verschiedene Zellen – die einen bauen den Knochen auf, die anderen bauen ihn ab. Die beiden sind in Balance.“ Das sei auch der Grund, warum Knochenbrüche heilen können. „Diese Dynamik nutzen wir aus.“
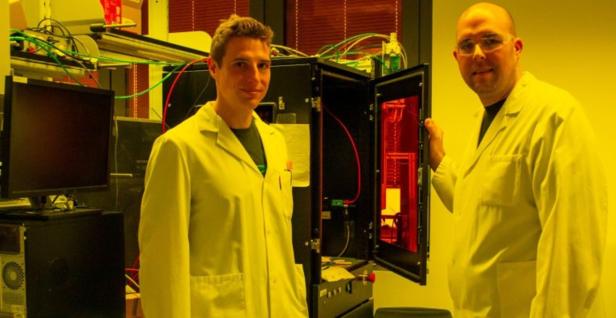
Stefan Baudis (rechts) in seinen Knochen-Labor
© TU Aigner
Die Forscher geben dem Körper an der verletzten Stelle ein passendes Gerüst, das dann von körpereigenen Zellen besiedelt und zum ganz normalen Knochen umgebaut wird. Versorgt werden diese Zellen durch Blutgefäße, die den Knochen durchziehen und den nötigen Stofftransport ermöglichen. Hergestellt wird das Gerüst mit der angesprochenen 3D-Druck-Technologie.
Denn die 3D-Drucker sind heute das Werkzeug der Wahl, wenn man keine massenproduzierte Serie identischer Objekte braucht, sondern passgenaue und maßgeschneiderte Knochenimplantate anfertigen muss.
Aus materialwissenschaftlicher Sicht ist das eine große Herausforderung: Das künstlich hergestellte Knochengerüst muss eine ganze Reihe von Anforderungen erfüllen: Es muss eine poröse Struktur haben, damit knochenaufbauende Körperzellen eindringen können und der Stofftransport funktioniert. Es muss fest, aber nicht zu spröde sein, damit es nicht sofort bricht. Es muss vom Körper in überschaubarer Zeit abgebaut werden, damit am Ende, wenn es durch natürlichen Knochen ersetzt wurde, vom Gerüst nichts mehr übrig bleibt. Außerdem sollen bereits Partikel aus Calciumphosphat im Gerüst eingebaut sein, die dann in das Knochenmaterial umgewandelt werden.
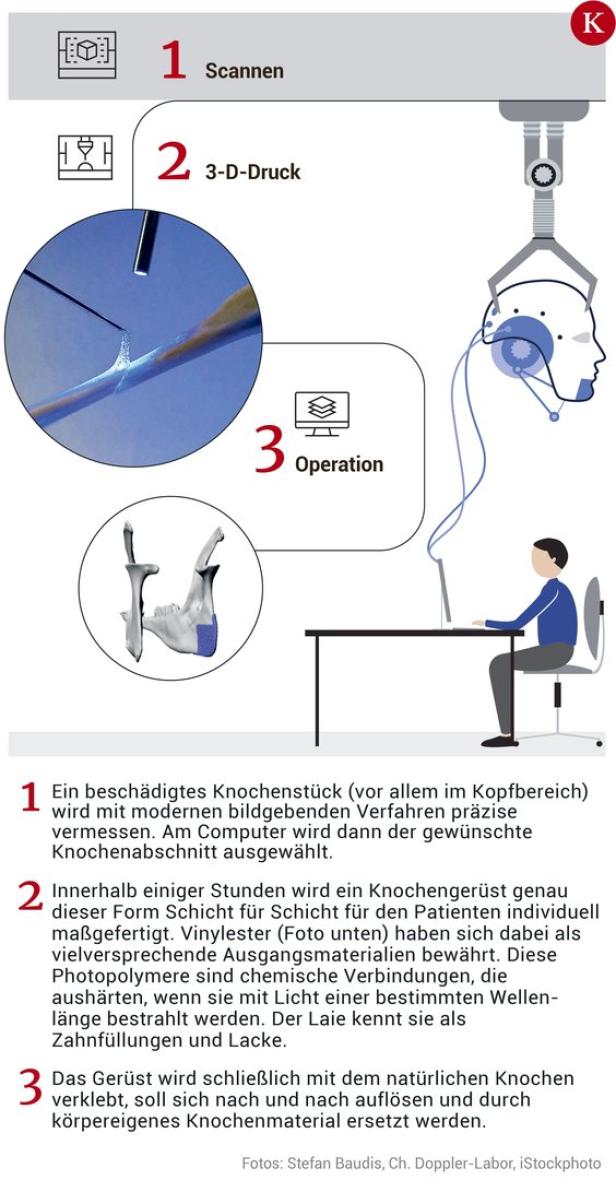
© Kurier-Grafik
Kettenreaktion
Gleichzeitig muss das Material 3D-Druck-tauglich sein: Es muss zunächst bei Raumtemperatur flüssig bleiben, bis es mit Licht der passenden Wellenlänge bestrahlt wird. Dadurch wird dann eine chemische Kettenreaktion ausgelöst, die das Material genau an den bestrahlten Stellen aushärtet.
„Wir wissen bereits viel über die Chemie der einzelnen Komponenten, die dafür nötig sind“, sagt Baudis. „Nun forschen wir am Fein-Tuning.“
Dass es funktioniert, weiß Baudis schon: „Wir haben das Ersatzteil bei Tieren eingesetzt.“ Schafe waren die Versuchskaninchen: Sie haben ein Stück neuen Kiefer bekommen. „Das Abbauen des Gerüstes funktioniert, die Knochenzellen wachsen.“ Dennoch bremst Materialwissenschafter Baudis überbordende Erwartungen auf komplette Skelette aus dem Drucker: „Es gibt Größenlimitationen. Wenn die Teile zu groß sind, bekommt man sie nicht lebendig. Titan-Ersatzteile sind für jene Bereiche, die großer Belastung ausgesetzt sind, nach wie vor alternativlos. Unser Plastik wird niemals die mechanischen Eigenschaften von Titan bekommen. Aber Kombinationen könnten interessant werden.“
Stichwort: Christian Doppler Labors
In den von der Christian Doppler Gesellschaft für jeweils sieben Jahre genehmigten CD-Laboren kooperieren Wissenschafter mit Unternehmen im Bereich anwendungsorientierter Grundlagenforschung. International gilt die Forschungsgesellschaft als Best-Practice-Beispiel für die Förderung dieser Zusammenarbeit.
Das Budget kommt dabei jeweils zur Hälfte von der öffentlichen Hand und den Unternehmenspartnern – das sind im Fall des neuen CD-Labors die deutsche Medizintechnik-Firma KLS Martin, der österreichische 3D-Druckspezialist Lithoz und die in Wien ansässige Trauma Care Consult Traumatologische Forschung Gemeinnützige Gesellschaft.
Kommentare