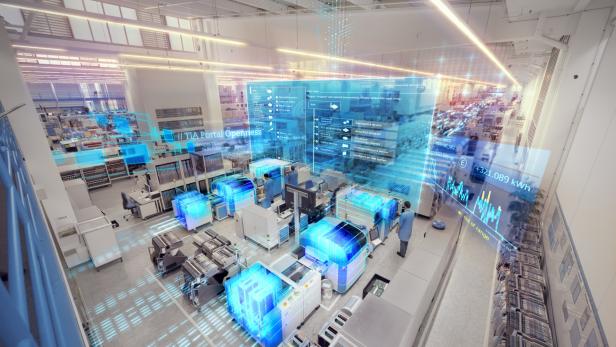
Wie „digitale Zwillinge“ die Auto-Entwicklung beschleunigen
Dieser Artikel ist älter als ein Jahr!
Die Automobilbranche gerät zunehmend unter Druck. Während Technologiekonzerne nahezu jedes Quartal neue Produkte auf den Markt werfen, muss man bei Autos oftmals mehrere Jahre auf ein neues Modell warten. Das Problem: Der Entwicklungsprozess, an dem oft deutlich mehr als tausend Mitarbeiter beteiligt sind, ist komplex und kostspielig. Doch obwohl die Entwicklungszyklen nach wie vor relativ lang sind, hat die Autobranche in den vergangenen Jahren erhebliche Fortschritte gemacht, wie Wolfgang Hesoun, Generaldirektor von Siemens Österreich, erklärt: „Früher brachten die großen Autohersteller etwa alle acht Jahre ein neues Modell auf den Markt. Heute ist der Zeitraum auf rund vier Jahre geschrumpft - inklusive individueller Kundenwünsche.“
Das sei vor allem auf die Digitalisierung zurückzuführen, durch die man in einer „virtuellen Fabrik“ bereits während der Entwicklung eines Fahrzeuges die entsprechenden Fertigungslinien entwerfen und programmieren kann. „Dank der digitalisierten Prozesse im Vorfeld können unsere Ingenieure von Linz aus für die Automobilindustrie weltweit Roboterstraßen programmieren und in Betrieb setzen. Allein für die Rohbaukarosserien werden bis zu 800 Roboter verwendet.“ Siemens ist das führende österreichische Unternehmen bei der Digitalisierung von Fabriken und dem Thema „Industrie 4.0“ .
Fehlerquote auf Weltrekord-Niveau gesenkt
Bereits 2015 eröffnete Siemens gemeinsam mit mehreren anderen Unternehmen und der TU-Wien eine Pilotfabrik in der Seestadt Aspern. Dort soll gemeinsam mit Klein- und Mittelunternehmen, die sich sonst die hohen Anfangsinvestitionen nicht leisten könnten, an der „Fabrik der Zukunft“ geforscht werden. Ein erstes positives Beispiel für die Digitalisierung: Der Siemens-Standort im bayrischen Amberg. Dort werden bereits seit einigen Jahren nahezu vollständig automatisiert speicherprogrammierbare Steuerungen (SPS) produziert, die gesamte Produktion wird digital nachverfolgt. Das Ergebnis: Die Fehlerquote beträgt lediglich 0,0012 Prozent, laut Siemens ein Weltrekord.
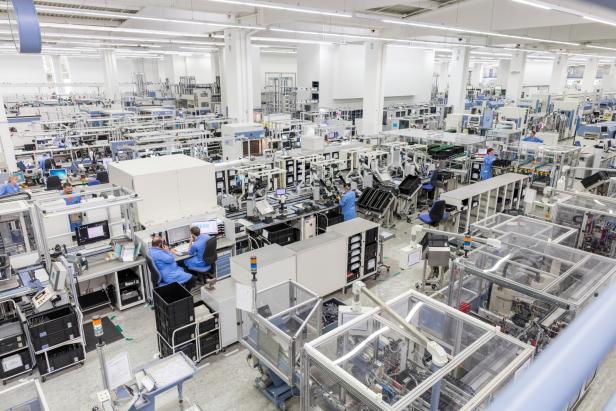
© Siemens
Schutz vor Hackern
Auch Zulieferer sollen Teil des Netzwerkes werden und erhalten mit dem „digitalen Zwilling“ in Echtzeit alle für die Fertigung relevanten Informationen. Das bedeutet, sie wissen sofort, wenn Bedarf besteht und können sich darauf vorbereiten. „Es gibt keine Pläne mehr, die per Post versandt werden, sondern alles ist online“, so Hesoun. Große Hoffnungen wird auch in das Thema „Machine Learning“ gesteckt. Die Software soll selbstständig Muster erkennen und sich diesen anpassen, um die Abläufe zu verbessern. So können beispielsweise die Betriebsdaten von Windrädern mit Wetterdaten verknüpft werden, um Anpassungen vorzunehmen und die Energieausbeute zu verbessern.
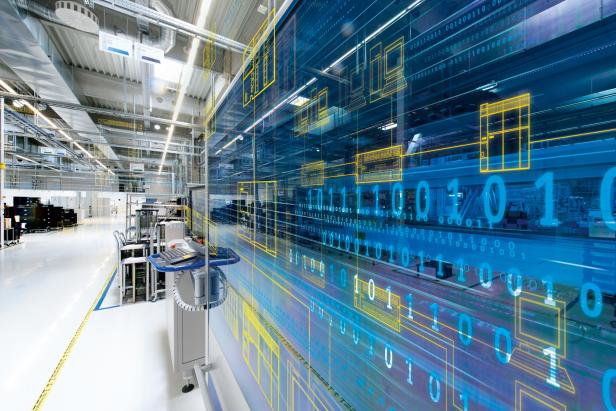
© Siemens
Die Tatsache, dass immer mehr Geräte mit dem Internet verbunden sind und über das offene Internet Daten miteinander austauschen, bietet aber ebenso viele Risiken wie Chancen. Für sensible Anwendungen, wie in der Industrie, will Siemens daher das selbst entwickelte „Web of Systems“ anwenden. Dabei werden die Maschinen weiterhin miteinander vernetzt, aber nur in Einzelfällen an das offene Internet angeschlossen. Die Daten werden lokal statt in der Cloud von Drittanbietern verarbeitet. So soll vor allem Datendiebstahl oder Manipulation durch Angreifer verhindert werden.
Keine Bedrohung für Jobs
Dass durch Industrie 4.0 ein Großteil der Jobs verloren gehen könnten, wie das Weltwirtschaftsforum in einer Studie prognostiziert, glaubt der Siemens-Österreich-Chef nicht. „Es ändern sich jedoch die Anforderungen an die Mitarbeiter und Aufgabenbereiche. Vor allem aber ändert sich die Produktionskapazität. Im Siemens-Werk im bayerischen Amberg haben wir 1.200 Mitarbeiter. Genauso viele wie vor 25 Jahren. Aber wir produzieren dort jetzt achtmal so viel wie damals.“
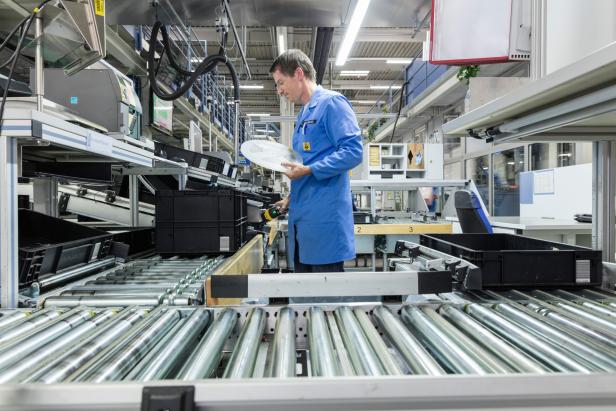
© Siemens
Dieser Artikel entstand im Rahmen einer Kooperation zwischen Siemens und der futurezone.
Kommentare