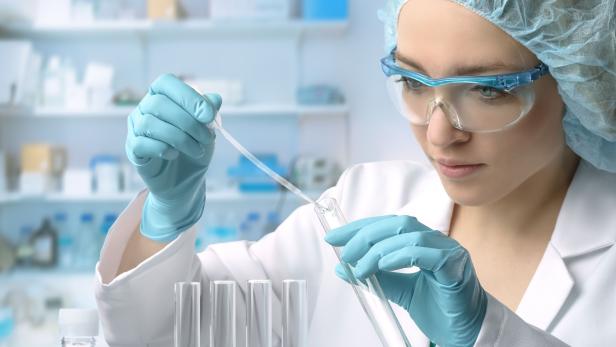
Digitalisierung soll personalisierte Krebsmedikamente ermöglichen
Dieser Artikel ist älter als ein Jahr!
Wohl kaum eine andere Branche hat derart lange Vorlaufzeiten wie die Pharma-Branche. Von einer Idee bis zum Verkaufsstart können mitunter bis zu 15 Jahre vergehen. Jeder noch so kleine Fehler kann dafür sorgen, dass ein Medikament deutlich später oder womöglich gar nicht zugelassen wird. Insbesondere die aufwändige lückenlose Dokumentation, umfangreiche klinische Studien sowie die laufende Prozessentwicklung verschlingt viel Zeit und Geld. Das Risiko ist auch für milliardenschwere Pharmakonzerne hoch. „Die Wahrscheinlichkeit, dass ein Medikament am Ende auf den Markt kommt, liegt bei durchschnittlich 14 Prozent“, sagt Daniela Buchmayr, Group Director Innovation & Application Development der deutschen GEA Group. Bei Kosten von 200 Millionen bis 1,3 Milliarden US-Dollar ein durchaus riskantes Unterfangen.
Von Millionen auf ein Stück
Um das Risiko zu minimieren, hofft nun auch die Pharmabranche auf die Digitalisierung von Prozessen. Viele Unternehmen der traditionsreichen Branche zieren sich aber noch vor der Industrie 4.0, wie Buchmayr erklärt: „Die Pharmabranche vermeidet gerne Risiken und wartet lieber ab, bis alle Pro und Kontra einer Technologie bekannt sind.“ Eine Zwischenlösung stellt die kontinuierliche Produktion dar. Dabei läuft die Produktion kontinuierlich weiter, die Qualitätskontrolle erfolgt dank digitaler Sensoren im laufenden Prozess. Dieser Vorgang ist deutlich flexibler und schneller als Batch-Prozesse, bei denen stets eine bestimmte Losgröße produziert und nach jedem Produktionsschritt geprüft wird.
“Dadurch muss man den Prozess immer anpassen, denn was mit einem halben Kilogramm funktioniert, funktioniert nicht automatisch mit 500 Kilogramm”, sagt Buchmayr. Durch die Vereinheitlichung der Produktion kann auch der Verbrauch der aktiven pharmazeutischen Wirkstoffe (API) deutlich gesenkt werden. Ein vor allem finanziell nicht unerheblicher Faktor. Ein GEA-Kunde konnte so beispielsweise den Bedarf von 1860 auf 385 Kilogramm senken und zwölf Millionen US-Dollar in der Forschungsphase einsparen. Der Marktstart kann ebenfalls bis zu ein Jahr früher erfolgen.
Partnerschaft mit Siemens
Nun will man mit der Hilfe von Siemens einen Schritt weitergehen, hin zur “personalisierten Medizin”. Dabei werden auf den Patienten maßgeschneiderte Medikamente und Therapien hergestellt - eine große Herausforderung, muss dabei doch auf die sogenannte “Losgröße Eins” produziert werden. “Mit der CAR-T-Zellen-Therapie wurde bereits eine entsprechende Lösung zugelassen. Das Rohmaterial, die T-Zellen, kommen vom Patienten selbst”, sagt Buchmayr. Diese Form der Krebstherapie ist zwar effektiv, aber relativ kostspielig. Bis zu einer halben Million US-Dollar können pro Behandlung fällig werden, zudem ist der Aufwand noch relativ hoch - auch weil der Prozess zu großen Teilen noch händisch abgewickelt werden muss.
“Um personalisierte Medizin für die breite Öffentlichkeit verfügbar zu machen, braucht es großflächige Automatisierung und Digitalisierung”, erklärt Buchmayr. Das sei nicht nur auf das eigene Unternehmen beschränkt, die ganze Branche müsse sich vernetzen und Standards schaffen. “Wir brauchen ein neues Ökosystem, wo alle Stakeholder zusammenarbeiten.” Aus diesem Grund hat man verschiedene Konsortien und strategische Partnerschaften gebildet, unter anderem mit Siemens. Im Zuge der nicht-exklusiven Partnerschaft sollen Standards geschaffen werden, die von der ganzen Pharmabranche genutzt werden können.
Österreich als Hotspot
“Wir verzeichnen zuletzt verstärkt Nachfrage von Firmen aus der Industrie, die ihre Prozesse digitalisieren wollen”, sagt Eckard Eberle, CEO von Siemens Process Automation. Allein in Mittel- und Osteuropa setzte man im Vorjahr fünf Milliarden Euro um. Weltweit beschäftigt man 20.000 Mitarbeiter, davon allein 10.000 in Österreich. “Rund tausend davon betreiben Forschung und Entwicklung im Prozessbereich”, so Eberle. Österreich soll dabei vor allem als “Hotspot für die Biotech-Branche” fungieren. Dabei lernt auch der Konzern dazu. “Unsere Kunden in der Pharmabranche wollen nicht wissen, wie man ein Auto baut, sondern wie man Inhaltsstoffe eines Medikaments möglichst rasch herstellen kann.”
Großes Einsparungspotenzial sieht er bei Dokumentation und Qualitätssicherung, das bis zu ein Viertel des Budgets verschlingt. Die Dokumentation ist in vielen Fällen nicht nur vorgeschrieben, sondern auch notwendig, um entsprechend auf sogenannte „Warning Letter“ der für Medikamente zuständigen US-Behörde FDA reagieren zu können. „Das kann sehr teuer werden, die internen Kosten können sich für das Suchen der Informationen auf bis zu eine Million US-Dollar hochschrauben“, sagt Buchmayr.
Personalisiertes Krebsmedikament
Siemens arbeitet unter anderem auch mit dem deutschen Biotech-Unternehmen BioNTech zusammen, das an einem personalisierten Krebsimpfstoff forscht. “Würde man diese Medikamente traditionell herstellen, würde ein Stück 100.000 Euro oder mehr kosten. Keine Versicherung dieser Welt würde das bezahlen”, erklärt Eberle. Obwohl das 2008 gegründete Unternehmen noch kein Medikament auf den Markt gebracht hat, mangelt es nicht am Interesse der Investoren. In einer Anfang 2018 abgeschlossenen Series-A-Runde wurden 225 Millionen Euro eingenommen, das Unternehmen wurde mit bis zu 2,5 Milliarden Euro bewertet. Um 2020 könnte der Impfstoff auf den Markt kommen. Erste klinische Studien waren vielversprechend: Acht von 13 behandelten Patienten blieben nach 23 Monaten tumorfrei.
Während junge Unternehmen wie BioNTech von Beginn an auf digitalisierte Produktion setzen können, stehen Pharma-Riesen oft vor großen Hürden. Siemens versucht den Digitalisierungsprozess so stark wie möglich zu vereinfachen. “Wir können eine Fabrik fast vollständig mithilfe von Fotos und Laserscans digitalisieren”, erklärt Kienlein. Dazu arbeite man unter anderem mit Bentley Systems, einem US-Entwickler von Konstruktionssoftware, zusammen. “Das ist deutlich schneller und effizienter als mit Papier-Dokumentation, die meist auch nicht vollständig ist.” Hat man einmal einen “digitalen Zwilling”, könne man diesen leicht mit zusätzlichen Daten anreichern und die Produktion verbessern.
“Führt kein Weg daran vorbei”
Um auch im eigenen Unternehmen mehr Bewusstsein für diese Unternehmenssparte zu schaffen, hat Siemens in seiner Unternehmenszentrale in Wien ein “Living Lab” eingerichtet. In diesem wird ein nahezu vollständig digitalisiertes Labor demonstriert. Jeder einzelne Schritt wird vollautomatisch dokumentiert und kann bei Bedarf im Protokoll nachvollzogen werden. Selbst das Entnehmen und Abwiegen der Bestandteile erfasst, auf manuelle Papier-Dokumentation wird vollständig verzichtet. “Das ist aber nicht nur ein Showroom, wir arbeiten auch hier”, erklärt Barbara Kavsek, Leiterin der Forschungsabteilung von Siemens Process Analytics & Sensors. Je nach Projekt arbeiten bis zu 15 Mitarbeiter an den “Living Lab”-Standorten und erproben die Siemens-Lösungen in der Praxis.
Obwohl das Labor einen simplen Eindruck macht, zeigen sich viele Unternehmen von der Einfachheit begeistert. An kontinuierlicher und personalisierter Produktion führe kein Weg vorbei, meint Johannes Khinast, Leiter des Institutes für Prozesstechnik an der TU Graz: “Die Pharmabranche muss mit den Fortschritten der Medizin Schritt halten. Wir werden in den nächsten Jahren dadurch einen revolutionären Wandel erleben.”
Dieser Artikel entstand im Rahmen einer Kooperation zwischen futurezone und Siemens. Die redaktionelle Hoheit liegt bei der futurezone.
Kommentare