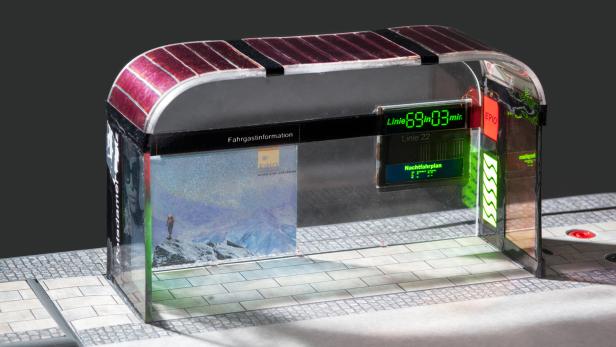
Deutsche Forscher drucken OLEDs und Solarzellen aus
Dieser Artikel ist älter als ein Jahr!
Forscher am Fraunhofer-Institut für Angewandte Polymerforschung (IAP) haben in Zusammenarbeit mit dem Anlagenbauer MBRAUN einen Drucker entwickelt, mit dem Organische Solarzellen und Organische Leuchtdioden (OLEDs) produziert werden können. Die Technologie verspricht eine kostengünstige Massenproduktion dieser zunehmend gefragten Elemente. Gleichzeitig erlaubt das Druckverfahren die Verwendung von flexiblen Trägermaterialien aus bestimmten Kunststoffen, was zu flexiblen Photovoltaik- und OLED-Elementen führt.
Der Drucker der deutschen Forscher soll vorerst zur Erstellung von OLEDs für Beleuchtungselemente und digitale Schilder - etwa zur Anzeige der Abfahrtszeiten in Haltestellen - verwendet werden. "Unser Verfahren funktioniert ähnlich wie ein Tintenstrahldrucker, nur eben mit anderer Tinte. In mehreren Schichten aus verschiedenen, flüssigen Lösungen organischer Materialien - mit Dicken zwischen 10 bis 300 Nanometer - werden die OLEDs aufgebaut", erklärt Christine Boeffel vom Fraunhofer IAP. Da die verarbeiteten Materialien empfindlich auf Feuchtigkeit und Sauerstoff reagieren, findet der Druckprozess unter Stickstoffatmosphäre statt. Für die industrielle Produktion eignet sich der aktuelle Prototyp noch nicht, Kleinserien für spezielle Einsatzgebiete sind aber realisierbar.
TV- und Smartphone-Schirme als Ziel
"Hochleistungs-OLEDs, wie in hochauflösenden Bildschirmen in der Unterhaltungselektronik, sind schwieriger zu drucken, hier ist das derzeit verwendete Vakuum-Aufdampf-Verfahren noch im Vorteil, da sehr komplexe Strukturen äußerst sauber gedruckt werden können", sagt Boeffel. Längerfristig sollen aber auch diese Displays im Druckverfahren hergestellt werden. Neben den Fraunhofer-Forschern arbeiten auch US-Wissenschaftler (die futurezone berichtet) und große Konzerne wie Samsung oder LG an den nötigen Technologien. Am Fraunhofer-Institut können derzeit maximal 150 x 150 Millimeter große Einzelelemente gedruckt werden, die Technologie ist im Prinzip aber skalierbar.
Der große Vorteil gedruckter OLEDs ist, dass sie deutlich günstiger produziert werden können. "Die Kosten für die Aufrechterhaltung des Vakuums im derzeitigen Prozess sind hoch, zudem gehen 50 Prozent - manche Kritiker sprechen sogar von bis zu 90 Prozent - des eingesetzten Materials beim Aufdampfen verloren. Beim Druckverfahren haben wir weniger als 10 Prozent Verlust", erklärt Boeffel. Die benötigten Materialien sind sehr teuer und kosten ein Labor zwischen 1.000 und 6.000 Euro pro Gramm. Im Industriemaßstab sind die Preise zwar niedriger, ein effizienterer Produktionsprozess lohnt aber allemal. In einem weiteren Schritt könnte sogar die Dünnschichttransistoren für die Steuerelektronik gedruckt werden, auch wenn die Kostenersparnis hier bei weitem nicht so hoch ist, wie bei den Leuchtkörpern selber.
Flexibles Glas
Auch für flexible Bildschirme eignet sich das Druckverfahren gut. "Gedruckt wird bei Raumtemperatur. Die 150 bis 200 Grad Celsius beim Trocklnungsprozess halten einige Kunststoffe gut aus. Zudem wird auch intensiv an flexiblem Glas gearbeitet, das nur 100 bis 200 Mikrometer dick ist und sich in einem Rolle-zu-Rolle-Druckverfahren verarbeiten lässt", erörtert Boeffel. Durch Rolle-zu-Rolle-Verfahren, bei denen Geschwindigkeiten von ein bis zwei Meter pro Minute realistisch sind, oder den Einsatz vieler, parallel arbeitender Druckköpfe, kann die Produktionszeit zudem enorm gesenkt werden. Damit könnten die gedruckten OLEDs auch billiger werden, als Flüssigkristall-Bildschirme (LCD). "Die Chancen dafür stehen gut", so Boeffel.
Organische Photovoltaik holt auf
Bei den Photovoltaikelementen wird es noch länger dauern, bis Solarzellen aus dem Drucker die Dächer von Häusern erobern. "Der Wirkungsgrad organischer Solarzellen erreicht unter Realbedingungen etwa die Hälfte der Werte, die Silizium-basierte Elemente schaffen. Es gibt aber laufend Verbesserungen", so Boeffel. Als Limit für eine Anwendung zur Stromerzeugung in Haushalten setzen Firmen ungefähr 10 Prozent Wirkungsgrad. Bis diese Schwelle mit gedruckten Solarzellen erreicht wird, werden laut der Fraunhofer-Forscherin aber noch Jahre vergehen.
Die Vorteile, die eine Produktion der Photovoltaikmodule im Drucker verspricht, wiegen die geringere theoretische Effizienz im Vergleich zu Silizium-Produkten aber auf . "Auch hier gibt es enormes Kosteneinsparungspoenzial, die organische Zellen sind zudem fast unabhängig vom Einstrahlungswinkel des Lichts und können senkrecht montiert oder in gewölbter Form gebaut werden. Die Produktion ist energieeffizienter und die Effizienz der Module nimmt nicht mit zunehmender Temperatur ab. Schließlich kann durch Schichten aus verschiedenen Materialien ein möglichst großer Teil des Lichtspektrums genutzt werden", so Boeffel.
Die Forschungsarbeit des Fraunhofer-Instituts und andere aktuelle Entwicklungen auf dem Gebiet der druckbaren Elektronikkomponenten werden auch beim "Print3Dfuture"-Kongress, der am 27.3. in Wien stattfindet, eine gewichtige Rolle spielen.
Kommentare