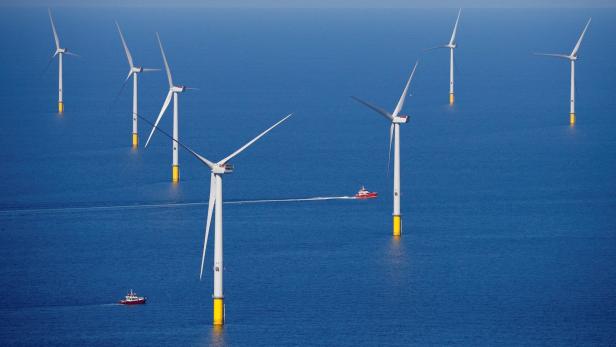
Revolutionäre Technologie verspricht günstigere Windräder
Dieser Artikel ist älter als ein Jahr!
Die meisten Offshore-Windräder werden als Monopiles errichtet. Dabei wird ein riesiger Stahlzylinder in den Meeresboden gerammt. Auf dem Teil, der dann aus dem Meer herausragt, wird ein sogenanntes Transition Piece aufgesetzt. Auf dieses kommt dann das eigentliche Windrad.
Das Zusammenschweißen des Stahls, um den Zylinder für einen Monopile zu kreieren, ist zeit- und kostenaufwändig. Ein Konsortium aus mehreren Unternehmen konnte nun erstmals dafür Elektronenstrahl-Schweißen nutzen, was viele Vorteile bringt.
Lokales Vakuum ermöglicht das Schweißen riesiger Bauteile
Üblicherweise werden Monopiles im Unterpulververfahren verschweißt. Das Elektronenstrahl-Schweißen wäre hier schneller und günstiger. Allerdings muss dabei in einem Vakuum geschweißt werden. Eine Vakuumkammer ist aber teuer und bietet nur begrenzt Platz.
Das Konsortium hat deshalb eine neue Technologie namens Ebflow genutzt. Diese wurde von Cambridge Vacuum Engineering entwickelt, das Teil des Konsortiums ist. Ebflow basiert auf dem Elektronenstrahl-Schweißen. Anstatt alles in ein Vakuum zu verfrachten, entsteht das Vakuum nur um die Naht, die geschweißt wird. Dadurch sei es erstmals möglich, Elektronenstrahl-Schweißen für selbst die größten Monopiles zu nutzen.

Wir würden hier gerne ein Youtube Video zeigen. Leider haben Sie uns hierfür keine Zustimmung gegeben. Wenn Sie diesen anzeigen wollen, stimmen sie bitte Youtube zu.
Schweißnähte sind gleichwertig oder besser als bisherige Methoden
Im Jänner 2023 wurde Ebflow erstmals erfolgreich bei Monopile-Komponenten genutzt. In einer Fabrik in Rotterdamm wurden 2,75 Meter lange Nähte geschweißt, um Zylinder mit 8 Metern Durchmesser zu erhalten. Diese hatten Wandstärken von 67 bis 85mm.
Der Vorgang und die Ergebnisse wurden von externen Inspektoren und der Regulierungsbehörde DNV überprüft. Die Schweißnähte wurden als „mindestens gleichwertig“, wenn nicht sogar besser als die üblichen Unterpulver-Schweißnähte bewertet. Einer der so entstandenen Zylinder wurde Teil eines Transition Pieces. Dieses soll Ende 2023 in der englischen Doggers Bank Windfarm installiert werden.

Wir würden hier gerne ein Youtube Video zeigen. Leider haben Sie uns hierfür keine Zustimmung gegeben. Wenn Sie diesen anzeigen wollen, stimmen sie bitte Youtube zu.
Schneller, billiger und sauberer
Laut dem Konsortium können mit Ebflow so zukünftig Monopiles mindestens 25-mal schneller geschweißt werden, als mit dem Unterpulver-Verfahren. Dabei wird mit Ebflow 90 Prozent weniger Energie verbraucht. Die Kosten werden um 88 Prozent reduziert, der CO2-Ausstoß um 97 Prozent.
In England nutzen derzeit über 90 Prozent der Offshore-Windräder Monopiles. Mit Ebflow könnten Windparks schneller und günstiger errichtet werden. Das würde laut dem Konsortium dabei helfen, die Energiewende zu beschleunigen. Außerdem hätten die Errichter der Offshore-Windparks die Option, die gesparten Kosten an ihre Kund*innen weiterzugeben – was zu geringeren Strompreisen führen könne.
Kommentare