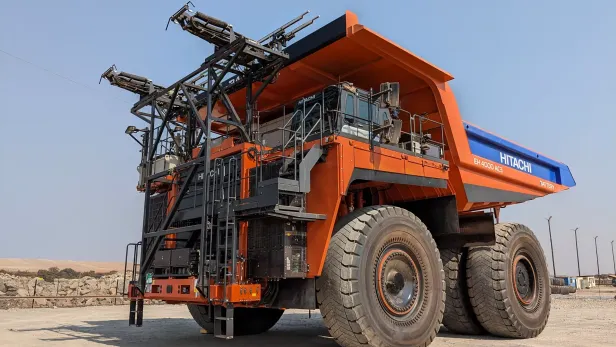
160 Tonnen unter Strom: Das ist der größte elektrische Kipplaster
So breit wie 4 SUVs (über 9 Meter), 14 Meter lang und unbeladen über 160 Tonnen schwer: Der Muldenkipper EH4000 des japanischen Herstellers Hitachi ist aufgrund seiner Ausmaße ein imposanter Anblick. Seit kurzem ist die Baumaschine zudem vollelektrisch unterwegs. Der laut dem Unternehmen “weltweit erste ultragroße vollbatteriebetriebener Muldenkipper” werkt in der achtgrößten Kupfermine der Welt im südafrikanischen Land Sambia.
➤ Mehr lesen: Gigantische Schaufler: Das sind die 10 größten Bagger der Welt
Es ist ein Probebetrieb, den der E-Muldenkipper in der Mine absolviert. An seiner Seite stehen mehrere dieselelektrische Muldenkipper desselben Models, die ebenfalls über einen elektrischen Antrieb verfügen. Die Energie dafür stammt allerdings aus einem Dieselmotor.
Oberleitung an, Dieselmotor aus
Dieser kann aber auch komplett abgeschaltet werden - nämlich wenn die Muldenkipper mit den etwa 4 Kilometer langen Oberleitungen in der Mine verbunden werden. Diese helfen dabei, die mehr als 200 Tonnen schwere Ladung über Rampen aus der Hauptgrube zu bringen. Ein Knopfdruck reicht, um die Stromabnehmer auszufahren, die an einem Gerüst an der Front des Fahrzeugs befestigt sind.
Solche E-Antriebe haben mehrere Vorteile. Ähnlich wie bei einem E-Auto wird die Beschleunigung und somit auch die Produktivität der tonnenschweren Baumaschinen dadurch verbessert. Mit 23 km/h können sie damit die 10 Prozent Steigung der Rampen bewältigen - ohne E-Antrieb wären sie nur mit 11 km/h unterwegs.
➤ Mehr lesen: E-Bagger und Elektrokran: Klimasünder Baustelle wird grün
Auch Treibstoff wird dadurch eingespart, was sich positiv auf die CO2-Bilanz auswirkt, wenn der Strom aus erneuerbaren Quellen stammt. Sambia ist für die Elektrifizierung des Bergbaus besonders attraktiv, denn 92 Prozent des Energiebedarfs des Landes werden durch grüne Energie gedeckt.
Größe der Batterie ist unbekannt
Beim vollelektrischen Muldenkipper werden Strecken ohne Oberleitungen nicht mit Energie aus Diesel überbrückt, sondern mit einer Batterie. Wie groß diese ist, ist nicht bekannt. Da die Batterie durch die Oberleitungen aufgeladen werden kann, muss die Kapazität nicht so groß sein, wie etwa bei einem E-Lkw, der Überlandfahrten bewältigen muss. Außerdem soll auch die Bremsenergie beim Bergabfahren wieder in die Batterie gespeist werden.
© Hitachi
Baumaschinen, die ihre Energie von Oberleitungen beziehen, gibt es in Europa nicht, weiß Dominik Dam von Zeppelin Österreich, dem Generalimporteur für Caterpillar Baumaschinen und Motoren. Hier würden einfach die großen Minen fehlen, für die sich solche Schwergewichte auszahlen würden.
Kleine Bagger und Radlader fahren schon elektrisch
Grundsätzlich hält die Elektrifizierung im Bereich der Baumaschinen aber auch in Österreich Einzug. Hier werden allerdings eher kleinere Bagger und Radlader mit Batterien ausgestattet. “Wir sprechen hier von Mini-Baggern mit 2 Tonnen Einsatzgewicht, die etwa innerstädtisch oder indoor eingesetzt werden”, sagt Dam.
Auch Volvo hat so einen elektrischen Mini-Bagger. Die Batteriekapazität liegt dabei mit 32 kWh nur bei der Hälfte eines Tesla Model 3.
Caterpillar arbeitet auch an rund 20 Tonnen schweren Baggern, die batterieelektrisch angetrieben werden. Die Batteriekapazitäten betragen hier zwischen 250 und 320 kWh.
In einem ähnlichen Bereich bewegt sich auch der elektrische Radlader L120H von Volvo. Hier ist die 240-kWh-Batterie im Heck des Fahrzeugs untergebracht und dient gleichzeitig als Gegengewicht für die große Schaufel.
Volvos L120H kann mit einer Batterieladung laut eigenen Aussagen 5 Stunden lang arbeiten. “Bei einem standardmäßigen Einsatz soll die Batterie einen Arbeitstag lang halten, bei intensiveren Einsätzen wird es entsprechend kürzer”, sagt Dam. In solchen Fällen lassen sich die Baumaschinen allerdings mit Schnellladegeräten wieder etwas aufladen, etwa in der Mittagspause.
Baumaschinen hängen am Kabel
Mit wesentlich kleineren Akkus kommen kabelgebundene Baumaschinen, die hauptsächlich stationär eingesetzt werden - etwa auf Recyclinghöfen. Sie beziehen ihre Energie über ein dickes Kabel, das mit einer Stromquelle verbunden ist. Das Kabel kann dabei wie bei einem Staubsauger aus dem Heck der Maschine aus- und wieder eingerollt werden. Den kleinen Akku benötigen sie, um von einer Stromquelle zur nächsten zu kommen. Alternativ kann dafür auch ein kleiner Dieselmotor verbaut werden.
Kabelgebundene Lösungen kommen etwa bei sogenannten Umschlagbaggern zum Einsatz, die Material von einem Ort an den anderen befördern. Sie können so in einem Radius von 50 bis 70 Meter um eine Stromquelle herum arbeiten. In Österreich kommt so eine Maschine etwa im Burgenland zum Einsatz, verrät Dam.
Dieselelektrische Fahrzeuge auf dem Vormarsch
Am schwierigsten zu elektrifizieren sind große Radlader und Schubbagger, wie sie etwa im Schotterabbau oder bei großen Erdbauprojekten zum Einsatz kommen. Hier geht die Richtung momentan hin zu dieselelektrischen Antrieben: “Solche Antriebe sind schon in diversen Maschinen verbaut und verzeichnen gute Erfolge. Die Fahrer sind überrascht, wie spritzig die Maschinen sind.”
Trotz der höheren Anschaffungskosten würden sie sich zudem im Laufe ihres Arbeitslebens auch finanziell auszahlen, denn sie sind produktiver, müssen weniger oft gewartet werden und verbrauchen je nach Hersteller zwischen 20 und 30 Prozent weniger Treibstoff. Es muss nämlich kein so leistungsstarker Dieselmotor verbaut werden, um die Elektromotoren mit Strom zu versorgen.
Forschung auch an alternativen Treibstoffen
Zumindest theoretisch könnten Verbrenner komplett CO2-neutral funktionieren - etwa mit auf Pflanzenöl basierten Kraftstoffen oder E-Fuels, die etwa aus CO2 und Wasser hergestellt werden. Verschiedene Baumaschinenhersteller, wie etwa Caterpillar und Liebherr, forschen zudem an Verbrennungsmotoren, die statt Diesel Wasserstoff nutzen können.
➤ Mehr lesen: Wie CO2-neutraler Treibstoff entsteht