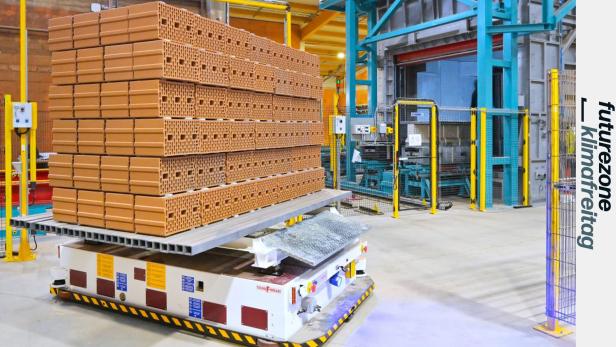
Die Ziegel werden auf automatisierten Wägen transportiert.
Weltweit größter elektrischer Ziegelofen spart Tonnen an CO2
Im Juli 2023 rollte der letzte mit Gas gebrannte Ziegel aus dem Wienerberger-Werk im oberösterreichischen Uttendorf. Der Stein ist ein Exemplar für die Vitrine - nicht, weil das Werk danach geschlossen wurde, sondern weil es zu 100 Prozent elektrifiziert wurde.
➤ Mehr lesen: Bakterien fressen CO2 und werden zu Bio-Beton
Statt des Gasofens, in dem die Ziegel zuvor gebrannt wurden, steht nun ein 80 Meter langer Elektroofen im Werk, der weltweit größte seiner Art. Im Moment läuft er im Probebetrieb, im kommenden Jahr soll er im Regelbetrieb 270 Tonnen Ziegel pro Tag produzieren, also etwa 100.000 Tonnen im Jahr. Das entspricht laut Wienerberger etwa 2.600 Einfamilienhäusern oder 3.000 Wohneinheiten.
Gesamten Prozess optimieren
Wenn man ein Ziegelwerk CO2-neutral machen will, reiche es nicht, einfach den Gasofen mit elektrischen Heizelementen auszustatten, sagt Andreas Kugi, wissenschaftlicher Leiter des Austrian Institute of Technology (AIT), das bei der Planung beteiligt war. “Da muss man weit darüber hinausgehen und den gesamten Prozess optimieren - das fängt bei einer CO2-neutralen Tonmischung an und endet bei den Wärmepumpen, die für das Trocknen eingesetzt werden.”
CO2-Fußabdruck der Ziegelindustrie
Laut einer Studie der Eidgenössischen Technischen Hochschule Lausanne ist die globale Ziegelproduktion für jährlich 1,1 Milliarden Tonnen CO2 verantwortlich, was in etwa einem halben Kilogramm CO2 pro Kilogramm produziertem Ziegel entspricht. Damit liegen die Emissionen dieser Industrie deutlich höher als die des globalen Flugverkehrs (0,7 Milliarden Tonnen im Jahr 2022).
So ein Tonziegel stößt beim Brennen aufgrund chemischer Reaktionen nämlich selbst CO2 aus, und zwar aufgrund des Kalkgehalts im Ton. Je weniger Kalkstein der Ton enthält, desto besser. Dem Ton wird auch Zellstoff und manchmal auch Kohle zugemischt, die im Ofen verbrennen und den Ziegel porös machen. So kann er ein Gebäude besser dämmen, die CO2-Emissionen erhöhen sich aber. Wienerberger nutzt stattdessen CO2-neutrale Sägespäne.
➤ Mehr lesen: Wie man durch Beton-Recycling Kohlendioxid speichern kann
Der Großteil der Emissionen fällt aber beim Trocknen und Brennen an. 90 Prozent des CO2-Ausstoßes können am Standort Uttendorf durch die Elektrifizierung eingespart werden. In Zahlen sind das 7.340 Tonnen pro Jahr. Das entspricht in etwa dem CO2-Ausstoß von über 7.000 Personen, die von Wien nach New York und zurück fliegen.
Elektroofen ist effizienter
Der neue Elektroofen spart im Vergleich zum Gasofen aber nicht nur CO2 ein, sondern auch 30 Prozent an Energie. Beim Gasofen muss nämlich ein Gas-Luft-Gemisch in den Ofen geleitet werden, damit die Verbrennung ablaufen kann. Dadurch entsteht ein Überdruck im Ofen, der abgelassen werden muss. Dabei geht wertvolle Wärme verloren. Beim Elektroofen entfällt das, die Wärme kann besser im Ofen gehalten werden. Außerdem ist der neue Ofen besser isoliert.
CO2-arme Ziegelherstellung
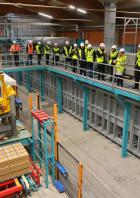
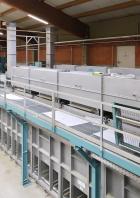
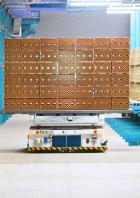
5 Bilder
Die Abwärme des Ofens wird gleichzeitig für die Wärmepumpen der Trocknungsanlagen genutzt. Vor dem Brennen müssen die nassen Tonziegel nämlich getrocknet werden. “Das benötigt ähnlich viel Energie wie das Brennen”, sagt AIT-Projektleiter Tilman Barz. Das Trocknen läuft bei Temperaturen von 80 bis 90 Grad Celsius ab, gebrannt werden die Ziegel etwa 20 Stunden lang bei knapp 1.000 Grad.
“Der gesamte Energieverbrauch der Anlage hat sich von 17 Millionen Kilowattstunden pro Jahr auf 11 bis 12 Millionen Kilowattstunden pro Jahr reduziert”, so Barz. Die Einsparung allein entspricht dem jährlichen Stromverbrauch von etwa 1.600 österreichischen Haushalten.
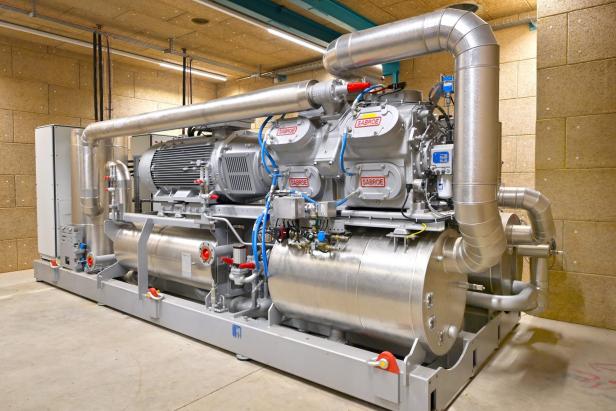
Eine Wärmepumpe am Standort.
© Manfred Fresl/Wienerberger
Um den für Ofen und Wärmepumpen benötigten Strom zum Werk zu bringen, musste allerdings extra eine Leitung zum Werk gelegt werden. “Das nächste Umspannwerk befindet sich 6 Kilometer entfernt in Mattighofen”, sagt Barz. Allein die Zuleitung und zusätzliche Infrastruktur am Standort hat 5 Millionen Euro gekostet. Bei einer Gesamtinvestition von 30 Millionen Euro ist das kein kleiner Anteil.
5 bis 10 Prozent der Energie stammt allerdings von der Photovoltaikanlage auf dem Werksdach. “Das ist kein kleiner Wert”, sagt Barz. Der Rest stammt zu 100 Prozent aus erneuerbarer Energie. Und obwohl Strom teurer ist als Gas, werden die Ziegel dank der Energieeinsparungen nicht teurer.
➤ Mehr lesen: Ziegel mit Strom erhitzen: Hitzebatterie speichert 1.800 Grad Celsius
Erfahrungen auf andere Industrien übertragen
Im Werk in Uttendorf werden nur sogenannte Hintermauerziegel produziert. Ziel ist es, auch andere Standorte zu elektrifizieren - Wienerberger betreibt mehr als 200 Werke weltweit - und ebenso Vormauer- und Dachziegel herzustellen. Hier muss zuvor allerdings noch ermittelt werden, wie der perfekte Elektroofen für diese Ziegelarten auszusehen hat. “Das ist recht aufwändig, im Tunnelofen gibt es 40 Zonen mit unterschiedlichen Temperaturen. Bei anderen Ziegeln ändert sich die Aufenthaltszeit im Ofen, die Stapelung, die Lücken zwischen den Ziegeln, zwischen denen die Luft zirkuliert - das alles muss berücksichtigt werden”, so Barz.
Die Erkenntnisse können allerdings auch in anderen Industrien eingesetzt werden, wo man Materialien brennen oder trocknen muss. In der Papierindustrie oder der Batterieproduktion gibt es ebenfalls Trocknungsprozesse, die von den Erfahrungen des AIT in diesem Bereich profitieren könnten, so Kugi.
Kommentare