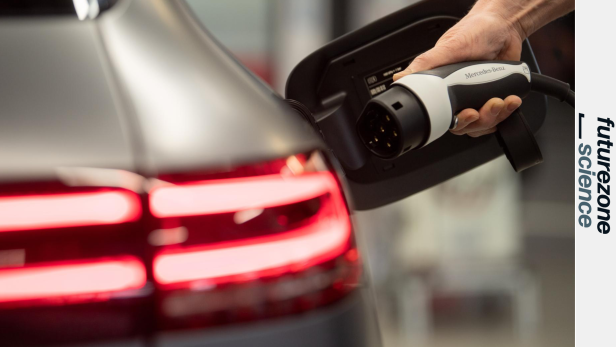
Wie Lithium-Ionen-Akkus für Elektroautos klimafreundlicher werden
Dieser Artikel ist älter als ein Jahr!
Der Verkehrssektor zählt zu den größten CO2-Emittenten. Elektrofahrzeuge können dabei helfen, den Ausstoß zu senken. Während sie im Fahrbetrieb klimaverträglicher sind als Verbrenner, benötigt die Herstellung der Lithium-Ionen-Batterien aber viel Energie. Wenn diese Energie nicht „grün“ erzeugt wurde, bedeutet das einen CO2-Ausstoß. Dies hat in der Vergangenheit allgemeine Zweifel an der Nachhaltigkeit von E-Autos geweckt.
Wie groß die Umweltbelastung konkret ausfällt, lässt sich aber nicht genau beziffern. Die Ergebnisse der Studien, die dazu bislang geführt wurden, variieren stark. Ein wesentlicher Teil der Treibhausgasemissionen entsteht jedenfalls durch den Strombedarf bei der Zellfertigung.
Aufbau einer Zelle
Elektroden
Die Kathode ist die negative Elektrode, die Anode ist die positive
Elektrolyt
Ist meist flüssig und leitet die Ionen von der positiven zur negativen Elektrode (entladen) und zurück (laden)
Separator
Ist eine Art Trennwand, die Kurzschlüsse vermeidet. Für Ionen ist sie durchlässig
Neutrale Herstellung
Innerhalb der EU strebt man künftig eine ökologischere Lösung an. Im Rahmen des Projekts „BatWoMan“ forscht das AIT Austrian Institute of Technology gemeinsam mit 6 Partnern aus der Forschung und Industrie an einer nachhaltigen, kosteneffizienten und CO2-neutralen Herstellung von Lithium-Ionen-Batteriezellen.
Im Fokus steht unter anderem die Optimierung des Füllprozesses des Elektrolyts, also des Ionenleiters, durch Elektroden auf Wasserbasis.
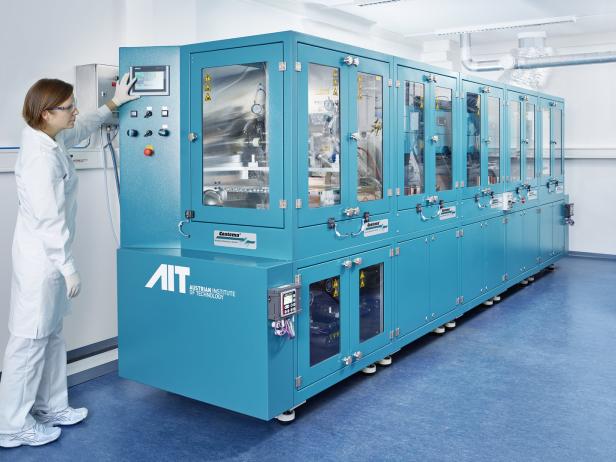
© AIT/Lang
„Stand der Technik ist, dass vor allem die Kathode mit toxischen Lösemitteln verarbeitet wird. Diese Mittel sollen durch Wasser ersetzt werden“, sagt die AIT-Forscherin und Projektleiterin Katja Fröhlich der futurezone. Alleine dadurch sei der ökologische Fußabdruck deutlich verbessert. Außerdem seien bei der Nutzung von Wasser weniger Bearbeitungsschritte nötig, was wiederum Energie spart.
3D-Elektroden
Beim Befüllen der Zelle wird der Elektrolyt unter Vakuum von einer Seite eingebracht. Dies passiere laut Fröhlich in mehreren Schritten. Dreidimensionale Elektroden sollen diesen Prozess deutlich verbessern. „Um das Ganze schneller und effizienter zu gestalten, wollen wir Strukturen hineinbringen, die eine Art Kapillarwirkung einbringen“, sagt sie.
Davon erwarte sich das Forschungsteam nicht nur, dass die Befüllung besser funktioniert, sondern auch generell weniger Elektrolyt zum Einsatz kommt. Denn dieser sei laut Fröhlich teuer und bestehe zum Teil ebenfalls aus Lösemitteln.
Verkürzte Trocknung
Da Lithium stark auf Luftfeuchtigkeit reagiert und eine Restfeuchte zu schnellem Leistungsverlust und vorzeitiger Alterung der Batterie führt, ist auch die sorgfältige Trocknung der Materialien ein wesentlicher Schritt in der Batterieproduktion. Die Elektroden der Zelle müssen in einem Trockenraum gegen Feuchtigkeit isoliert werden. Bei diesem Prozess entstehen ebenfalls ein hoher Energieverbrauch und Treibhausgas-Ausstoß.
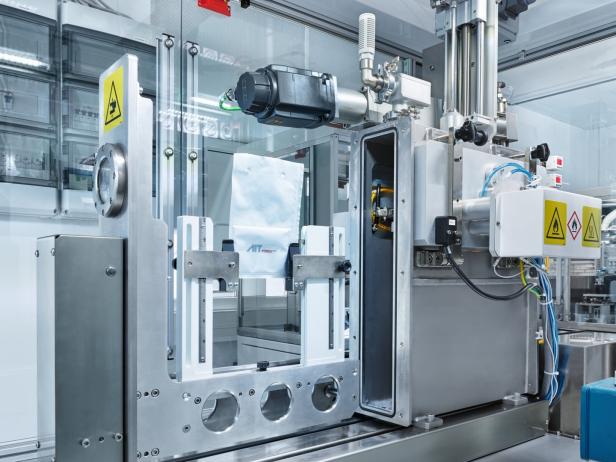
© AIT/Lang
„Wir verwenden auf der Anode und Kathode nicht nur Wasser. Wir schauen, dass wir generell den Anteil an Lösemittel – auch an Wasser – so stark reduzieren, dass man den Trockenschritt bei der Elektrodenfertigung verkürzen kann“, sagt die Batterieforscherin. Der Restfeuchtegehalt der Zellen sei dadurch zudem geringer.
KI-gestützte Plattform
Unterstützt wird das Vorhaben des AIT zusätzlich durch eine auf einer künstlichen Intelligenz (KI) basierten Plattform. Die soll die Nachhaltigkeit und Effizienz der neuen Produktionsprozesse abbilden.
„Es gibt diverse Bestrebungen auf globaler, aber auch auf EU-Ebene, dass man eine Art Batterie-Pass erstellt, wo diverse Informationen über die Batterie gespeichert werden können“, sagt Fröhlich und ergänzt: „Der Fokus ist, dass nicht nur hinterlegt wird, welche Materialien enthalten sind – das ist später zum Beispiel für das Recycling wichtig, wenn man die Materialien wieder separieren möchte – sondern auch, wie energieeffizient die Produktionsprozesse abgelaufen sind.“ Dies könne Hinweise über die Nachhaltigkeit der Zelle liefern.

Katja Fröhlich, AIT-Batterieforscherin
© AIT/Zinner
Weniger CO2
Die Laufzeit des Projekts beträgt 3 Jahre. „Im Moment sind wir dabei zu definieren, was kritische Produktionsparameter sind.“ Untersucht werde auch der Ursprung der Materialien und wie diese abgebaut werden.
BatWoMan werde auf Ebene der Batteriezellen-Erzeugung mit den vorgeschlagenen Prozessen schätzungsweise zu einer Senkung der CO2-Emissionen um etwa 50 Prozent führen. „Bei den Kosteneinsparungen ist man sogar noch ein wenig höher“, sagt Fröhlich.
Wann die nachhaltige Batterie betriebsbereit sein wird, ist aber nicht eindeutig vorherzusagen. Dies hängt vorrangig davon ab, wie die Entwicklung vom Markt übernommen wird. Das Projekt wurde im Rahmen des Forschungs- und Innovationsprogramms Horizon 2020 der EU gefördert.
Dieser Artikel entstand im Rahmen einer Kooperation zwischen AIT und futurezone.
Die keramische Feststoffbatterie kommt
Bei Lithium-Ionen-Akkus kommen unter anderem die Rohstoffe Kobalt und das teurere Lithium zum Einsatz, deren Abbau kritisch und energieintensiv ist und die CO2-Emissionen steigen lässt. Eine Alternative bieten unter anderem keramische Festkörperbatterien.
Das Fraunhofer Institut für Keramische Technologien und Systeme (IKTS) hat beispielsweise eine solche Feststoffbatterie namens Cerenergy entwickelt, die auf Kochsalz und kleinen Mengen Nickel basiert.
Kathodengranulat
Anders als Lithium kommt Natrium in großen Mengen in Form von Kochsalz vor und zählt zu den günstigen Rohstoffen. Lithium, Kobalt, Graphit und Kupfer – Rohstoffe, die von Lieferengpässen betroffen sind oder zunehmend teurer werden – sind in der Festkörperbatterie nicht enthalten.
Kochsalz und Nickel werden zu einem Kathodengranulat verarbeitet. Dieses wird in ein Keramikrohr gefüllt, das als Elektrolyt dient und die Natrium-Ionen leitet. Das Keramikrohr erfüllt somit die gleiche Aufgabe wie ein herkömmlicher, flüssiger Elektrolyt in einer Lithium-Ionen-Batterie. Die keramischen Festkörperbatterien können im Gegensatz dazu nicht explosionsartig abbrennen („Thermal Runaway“), da der Elektrolyt nicht brennbar ist.
Damit zwischen dem Kathodengranulat und dem festen keramischen Elektrolyt-Rohr Kontakt besteht, kommt für die positive Elektrode die geschmolzene chemische Verbindung Chloraluminat zum Einsatz.
Kommerzialisierung
Die keramischen Festkörperbatterien wurden bereits in stationären Batteriemodulen getestet und stehen nun vor der Kommerzialisierung. Das Fraunhofer IKTS hat sich dafür mit der Altech Group zusammengeschlossen.
Die Produktionsanlage soll 10.000 Batteriemodule pro Jahr mit einer Kapazität von je10 Kilowattstunden produzieren. Der Preis pro Modul wird sich schätzungsweise zwischen 7.000 und 9.000 Euro belaufen. Insgesamt sollen mit diesem Produkt bis zu 40 Prozent der Produktionskosten eingespart werden.
Kommentare