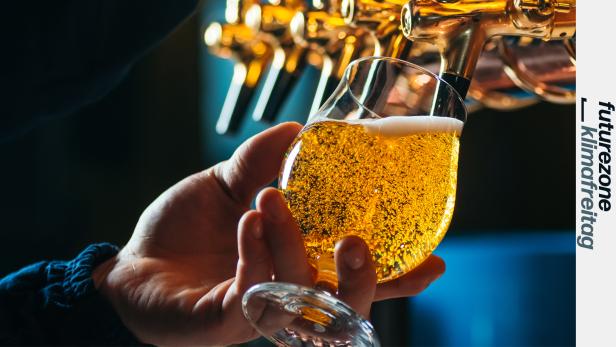
Beim Bierbrauen wird immer öfter auch auf die CO2-Bilanz geachtet
Bierbrauen ohne Klima-Kopfweh
Um aus Gerstenmalz und Hopfen ein Getränk herzustellen, das rund 60 Prozent der Österreicher*innen regelmäßig konsumieren, braucht es viele Produktionsschritte und viel Energie. Bislang wurde vor allem Erdgas dafür eingesetzt, um Maische und Würze auf dem Weg zum fertigen Bier zu erhitzen.
Abgesehen von der Wärmeerzeugung entstehen bei der Bierproduktion aber auch an anderer Stelle viele Treibhausgasemissionen, etwa bei der Anlieferung von Zutaten, bei der Verpackung oder bei der Verwendung von Kohlendioxid. Viele Bierhersteller wollen Emissionen reduzieren, wegen des Klimaschutzes, aber auch aus wirtschaftlichen Gründen.
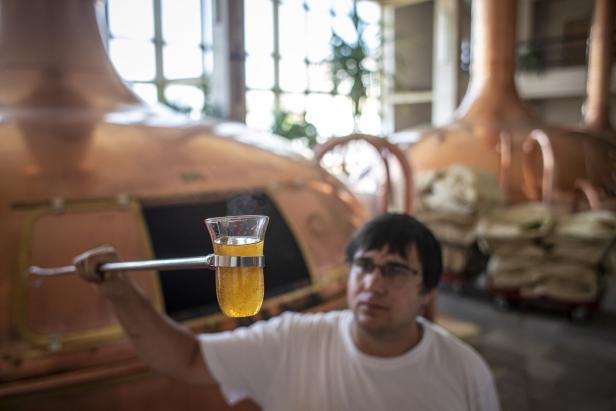
Im Sudhaus wird die Würze hergestellt, dafür braucht es viel Wärmeenergie
© EPA/MARTIN DIVISEK
Fernwärme statt fossilen Treibstoffen
Die Brauerei Murau bezieht Wärme für ihre Herstellungsprozesse in Form von heißem Wasser aus einem nahen Biomassekraftwerk. „Vor zwei Jahren waren über 90 Prozent der Brauereien von Erdgas abhängig. Durch die Gaskrise haben einige Mitbewerber angefragt, ob sie bei uns brauen können“, erzählt Geschäftsführer Sepp Rieberer. „Früher haben wir 900.000 Liter Erdöl gebraucht, um heißen Dampf zu erzeugen. Jetzt bleibt die Wertschöpfung bei unseren Landwirten.“ Was im Biomassekraftwerk verheizt wird, kommt aus dem direkten Umkreis von Murau.
➤ Mehr lesen: Fernwärme: So schlagen wir uns im europäischen Vergleich
In der Brauerei Göss in Leoben wird Fernwärme von einem nahen Sägewerk bezogen. Dazu wird Biertreber, ein Abfallstoff aus der Produktion, vergoren und zu Biogas gemacht. Strom für die Produktion wird durch eine große Photovoltaikanlage am Brauereigelände teilweise selbst erzeugt, sagt Gabriele Straka von Brau Union. Bis 2030 soll der Standort komplett CO2-neutral werden. Das sind Vorgaben von Heineken. Gösser Bier und Mutterkonzern Brau Union gehören zu dem niederländischen Unternehmen.
Elektrifizierung reduziert Dampfbedarf
Heineken betreibt derzeit eine große Dekarbonisierungsoffensive und hat sich dafür Hilfe geholt. Siemens analysiert den Energiebedarf von Brauereien, bringt Verbesserungsvorschläge und setzt diese um. Unter anderem werden bestimmte Herstellungsprozesse, für die man bisher meist heißem Dampf verwendet hat, elektrifiziert. Das sei unter anderem durch den Einsatz von Wärmepumpen möglich, erklärt Christoph Pacher von Siemens. Eine Umgestaltung der Produktion sei kostenaufwendig. Relativ schnell rentiere sich die Rückgewinnung von CO2. Das Gas entstehe beim Gärprozess, man kann es einfangen und später im Herstellungsprozess dem Bier wieder – als Kohlensäure – zuführen, anstatt zugekauftes CO2 zu verwenden. „In Österreich wird das auch meist so gemacht“, sagt Pacher.
Neben der Dekarbonisierung der Produktion achten Brauereien auch vermehrt auf den Transport. Die Brauerei Murau testet den Einsatz von Wasserstoff- und batterieelektrischen Lastwägen, der Pkw-Fuhrpark ist bereits elektrifiziert. Heineken setzt Elektro-Lkw bereits beim Biertransport zwischen den Niederlanden und Deutschland ein.
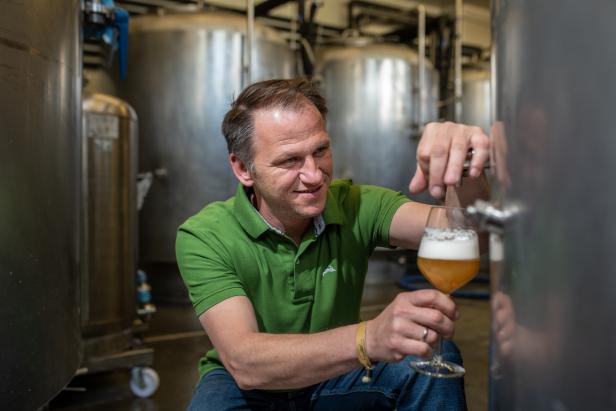
Alois Gratzer produziert das Gratzer Naturbier mit Rücksicht auf regionale Wertschöpfung und ökologische Verträglichkeit
© Rene Strasser
Kompensation von Emissionen
Beim Vermeiden von Emissionen müsse man einen weiten Blick haben, sagt Alois Gratzer, der in einer kleinen Brauerei im steirischen Kaindorf das Gratzer Naturbier produziert. „Unsere Gerste kommt von 5 Landwirten aus der Region. Das verkürzt die Transportwege wesentlich.“ Für die Feldfrüchte zahle man einen Preis, der es den Landwirten ermögliche, auf Dünger und Pestizide weitgehend zu verzichten und dadurch weniger Ernte zu erzielen. „Unsere Wasserqualität hat sich dadurch merkbar verbessert“, meint Gratzer.
Die Prozesswärme liefern Hackschnitzel, aber auch Gas. Dafür werden Emissionen durch Investitionen in ein Humusaufbauprojekt kompensiert. Die nährstoffreiche Erde bindet CO2 im Boden. Um Emissionen zu vermeiden, entschloss sich Gratzer aber auch dafür, Mehrweg-Glasflaschen mit Bügelverschluss zu verwenden: „Das ist der einzige Verschluss, den man nicht wegschmeißen muss.“
Kommentare