
Wiener Firma entwickelt medizinische Filtermasken mit 3D-Druck
Dieser Artikel ist älter als ein Jahr!
Während der Corona-Krise hat die Medizin das Potenzial von 3D-Druck entdeckt. Damit können schnell Bauteile produziert werden, aus einer Taucherbrille wird eine Beatmungsmaske und an der TU Graz druckt man Gesichtsschutz aus. Viele Firmen wollen während der Corona-Krise dem medizinischen Personal helfen, das immer noch mit Versorgungsengpässen zu kämpfen hat. Eine davon ist die Wiener Firma Cubicure. Normalerweise verkauft sie 3D-Drucker, jetzt stellt sie wiederverwendbare Halbmasken her, um das medizinische Pflegepersonal in Spitälern zu unterstützen.
„Würden wir einfach eine Vorlage aus dem Internet nehmen, könnten wir innerhalb von 24 Stunden eine Maske ausdrucken“, sagt Kristina Hager, die in der Sales-Abteilung des Start-ups arbeitet. Die Halbmasken sind aus festem schwarzem Kunststoff gefertigt, sind aber sehr leicht. Der Vorteil gegenüber herkömmlichen Masken: „Unser Material kann man sterilisieren und wiederverwenden. Andere Masken sind nur für den Einmalgebrauch geeignet und das sehen wir nicht als brauchbares Konzept für eine Krisensituation.“ Nur das eingelegte Filtermaterial müsste regelmäßig gewechselt werden, sagt Hager. Das ist derzeit eine Herausforderung, denn dieses Material ist schwierig zu bekommen. Hochwertige Filtertextilien sind jedenfalls eine Voraussetzung, um eine FFP2- oder FFP3-Klassifizierung zu erhalten.
Massenproduktion und Individualisierung
Für die Massenproduktion arbeitet das Unternehmen mit einem Kunststoffverarbeiter aus Deutschland zusammen. Dort können die Masken in hohen Stückzahlen im Spritzguss-Verfahren hergestellt werden. Mit dem 3D-Druck werden eher kleine und mittelgroße Serien oder Einzelstücke produziert.
Das Material, die Designs und Prototypen dafür werden bei Cubicure entwickelt. Am Standort im Tech-Park Vienna stehen nicht nur zahlreiche 3D-Drucker, die ständig neue Versionen der Masken ausdrucken. In einem eigenen Labor arbeiten Forscher stetig an neuen Materialien. So kann sofort geprüft werden, ob ein Kunststoff für einen Einsatzzweck geeignet ist. Das macht die Firma unabhängig von Anwendungsgebieten, weshalb ein schnelles Umdenken während der Corona-Krise möglich war: „Wir haben den Mangel gesehen und wir haben die Kapazitäten, um zu helfen. Wir haben daher entschieden, die Zeit aus dem Rückgang des Tagesgeschäfts in die Maskenentwicklung zu investieren“, so Hager.
"Hot Lithography"
Für die Halbmasken wird einer der vier Serienkunststoffe des Start-ups verwendet: „Normalerweise dauert es 6 bis 12 Monate, bis ein industriereifes Material entwickelt ist. Da unser Material die Anforderungen für den Maskeneinsatz bereits erfüllt, konnten wir schnell auf dieses Feld umsteigen“, erklärt Hager.
Dazu wird mit der „Hot Lithography“-Technik gedruckt, ein in Wien entwickelter 3D-Druckprozess, den sich das Unternehmen mehrfach patentieren ließ. Hierbei wird das Material auf bis zu 120 Grad erhitzt und in dünnen Schichten aufgetragen. Ein Präzisionslaser belichtet das Material an den vorgesehenen Stellen. Dort härtet der Kunststoff unmittelbar aus und bleibt an der Bauplattform haften. So wird das Material bis zur fertigen Maske aufgeschichtet. Diese wird dann noch von überschüssigem Kunststoff gereinigt und kann sofort eingesetzt werden.

Wir würden hier gerne ein Youtube Video zeigen. Leider haben Sie uns hierfür keine Zustimmung gegeben. Wenn Sie diesen anzeigen wollen, stimmen sie bitte Youtube zu.
Diese Technik erlaubt es, besonders detaillierte Bauteile herzustellen, da man mit einer Strukturgenauigkeit von 25 Mikrometern arbeiten kann. Denn das Hauptgeschäft des von TU-Wien Absolventen gegründeten Start-ups ist nicht die Fertigung von Produkten, sondern der Verkauf der industriellen 3D-Drucker und der zugehörigen Materialien.
Individuelle Masken
Zukünftig wäre es denkbar, dass Cubicure einzelne Masken genau auf die Gesichtsform einer Person anpasst. Generell sind Schutzausrüstungen wie Halbmasken häufig für Männer designt, allerdings arbeiten vor allem Frauen in medizinischen Pflegeberufen und sind dort oft auf das Tragen solcher Masken angewiesen. Die Individualisierung hat aber auch ihren Preis. Hager rechnet damit, dass die 3D-gedruckten Masken rund 100 Euro pro Stück kosten werden. Anders als Einwegmasken könnte man sie bis zu ein Jahr lang nutzen.
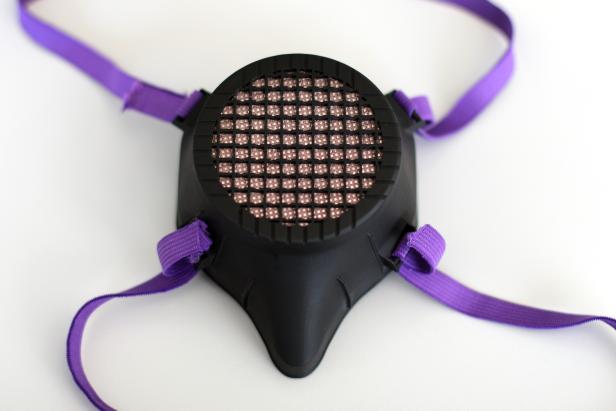
© Franziska Bechtold
Eine persönlich angepasste Maske könnte so erhöhte Sicherheit bieten – vorausgesetzt, sie erfüllt die Anforderung der Zertifizierungsstelle. „Die größte Herausforderung bei der Fertigung der medizinischen Masken ist eine gute Dichtheit. Bei FFP-Masken dürfen keine Aerosole durchkommen. Es gibt zwar bereits viele einfache 3D-Modelle für Masken im Internet, unser Designteam hat aber schnell festgestellt, dass die Anpassung an das Gesicht wirklich präzise sein muss“, sagt Hager. Dafür arbeitet das Unternehmen mit Menschen aus dem Gesundheitssektor zusammen, die den Tragekomfort testen und bei der Abdichtung beraten.
Die Masken-Entwicklung sieht das Unternehmen mittelfristig als Türöffner für die Medizintechnik. „Wir wollen zeigen, was mit 3D-Druck möglich ist. Vor allem auch wie schnell Projekte umgesetzt werden können und dass die bereits zur Verfügung stehenden Materialen für die Medizintechnik geeignet sind. Zusätzlich erhält man ein enormes Individualisierungspotenzial in der Fertigung. Wir werden in diesem Sektor noch viel Innovation sehen“, sagt Hager.
Kommentare