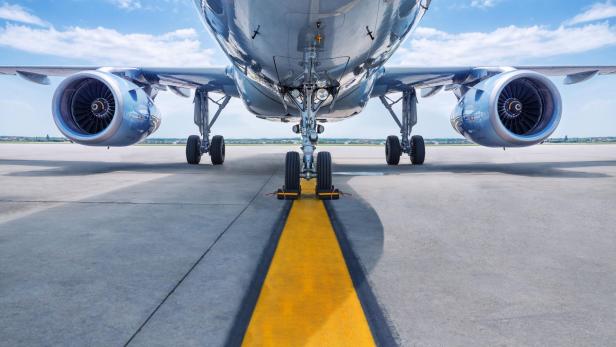
Start-up prüft Flugzeugbauteile berührungslos
Dieser Artikel ist älter als ein Jahr!
Dass Flugzeuge in der Luft mit Vögeln zusammenprallen, kommt vor. Für die Vögel endet ein solcher Crash meist fatal. Aber auch die Flugzeuge können Schaden nehmen. Und der ist nicht notwendigerweise sichtbar. Unter der Oberfläche können sich beispielsweise die Lagen von Faserverbundstrukturen trennen und die mechanische Festigkeit kritischer Teile des Flugzeugs beeinträchtigen. Das Welser Start-up voidsy hat ein kompaktes Messgerät entwickelt, mit dem solche Schäden schnell erkannt werden können.
Mit Maßen von 420x270x130 Millimeter und einem Gewicht von weniger als 5 Kilogramm ist es auch sehr kompakt. "Es kann von Prüfer*innen im Trolley transportiert und im Handgepäck mitgeführt werden", sagt Holger Plasser, der das Start-up gemeinsam mit Günther Mayr, Gernot Mayr und Gregor Thummerer im vergangenen Jahr gegründet hat.
Berührungslos
Weil bei der Material- und Bauteilprüfung die aktive Thermographie zum Einsatz kommt, funktioniert das Prüfverfahren berührungslos. Dabei wird Licht auf ein Bauteil gestrahlt und die Oberflächentemperatur gemessen. Bei einem fehlerfreien Bauteil fließt die Wärme gleichmäßig ins Innere. Weist das Material einen Defekt auf, kommt es zu einem Hitzestau. Die Ergebnisse der Temperaturmessung werden mathematisch so umgerechnet, dass eine dreidimensionale Darstellung des Defekts modelliert werden kann und daraus die thermische Tomopraphie resultiert.
Die Unschärfe nehme mit zunehmender Tiefe zu, sagt Plasser. Weil aber aus dem Rauschen Informationen extrahiert werden können, lassen sich mit dem Verfahren bis zu 1,5 Zentimeter Tiefe Aussagen über den Zustand der Materialien treffen. Im Vergleich mit anderen thermographischen Verfahren konnte das Start-up die Genauigkeit um den Faktor 2 verbessern.
Voidsy 3D V-ROX
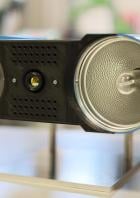
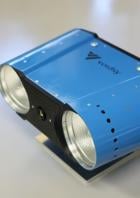
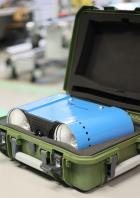
4 Bilder
Anders als bei den Bauteil- und Materialprüfungen gängigen Ultraschallverfahren, die auch nicht kontaktlos sind, ist bei der Thermographielösung auch kein Koppelmedium, wie etwa Gel oder Wasser, notwendig.
Von der Flugzeugtragfläche bis zum Fahrradrahmen
Zum Einsatz kommen soll das Verfahren in der Luft- und Raumfahrt, für Inspektionen und für Qualitätsprüfungen in der Produktion. Auch die Porosität von Materialien könne mit der Lösung bestimmt werden, sagt Plasser. Interesse gibt es auch aus der Automotivebranche sowie dem Sport- und Freizeitbereich. Dort sollen mit dem Messgerät etwa Qualitätsprüfungen von spritzgegossenen, kurzfaserverstärkten Kunststofffahrradrahmen durchgeführt oder die Schlageinwirkung auf Bootsrümpfe oder Jetskis geprüft werden, erzählt Plasser.
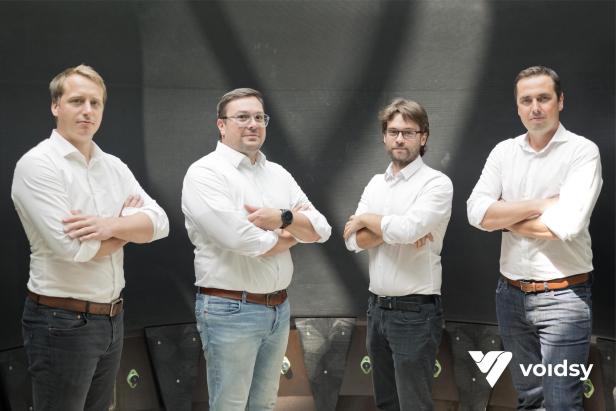
Voidsy-Gründer: Gregor Thummerer, Holger Plasser, Gernot Mayr und Günther Mayr (v.l.n.r.)
© Voidsy
Seit Ende Dezember ist ein Prototyp des Messgeräts bei Pilotkunden im Einsatz. Mit ihnen gemeinsam soll es zur Serienreife geführt werden. "Wir gehen intensiv auf die Anforderungen der Unternehmen ein und wollen das Feedback in das Produkt einfließen lassen", sagt Plasser. 2025 soll das Messgerät schließlich auf den Markt kommen. Bis dahin muss laut dem Gründer auch die Software der Lösung noch verbessert werden.
Auch mit Herstellern von automatisierter Prüftechnik arbeitet das Start-up zusammen. Das Gerät kann etwa an einen Roboter angebracht werden, der große Bauteile, etwa Tragflächen von Flugzeugen, abfährt und danach die Ergebnisbilder zusammensetzt. Die modulare Integration in bestehende Prüfvorrichtungen und der gemeinsame Vertrieb sei ein "Türöffner" in der Branche, sagt Plasser.
Aus den Pilotkundenprozessen erwirtschaftet das Start-up bereits erste Umsätze. Finanziert wurde es aus Eigenleistungen der Gründer sowie Förderungen der Förderbank Austria Wirtschaftsservice (aws).
Dieser Artikel entstand im Rahmen einer Kooperation zwischen futurezone und Austria Wirtschaftsservice (aws).
Kommentare